I just poured ingots -- long ones so I wouldn't mix it up with my other stock in muffins.
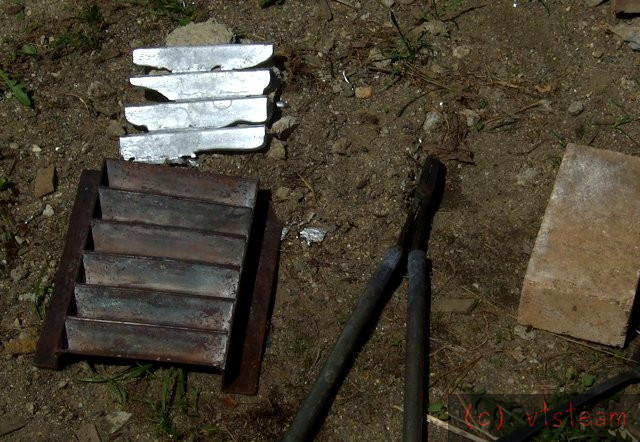
Hi Seadog, welcome aboard!

Yes it sure did dissolve easily after all.
Rob, I haven't tried machining it yet, but will. I did snap one of the thinner ingots in half in the vise with a big hammer. It definitely breaks rather than bends. It feels hard, and rings hard. But it isn't any harder than a piece of 6061 I tried scratching it on. Also, no harder than a cast aluminum part on my Gingery lathe (pure melted pistons). Not s hard as zamak za-2. But it did scratch some of my newer stock of ingots (also pistons). Not much harder than them, though. I'm guessing the difference may be due to aging of the castings and 6061, possibly making them harder, while the newer ingots were scratched.
Anyway, not a big improvement in hardness. Nevertheless just handling it, it seems hard and tough -- just a subjective impression. I don't know why that is.
It saws readily with a hacksaw. No tendency to smooth over or gum up.
It files easily, and again seems harder under the file subjectively.
Unfortunately I can't compare it to my other cast aluminum for strength and brittleness, since I don't have a similar section in those others for the vise break test. I did try some 6061 of similar thickness which seemed much tougher. But it's a good tempered extrusion alloy compared to cast, so that wasn't unexpected. The big question is, is this a better casting mix than just straight pistons?