.... With minimal help from me

It will save a lot of typing if the item I needed to make is shown first:
It’s a cam to push a half nut up against the leadscrew of my baby Perris lathe, like those shown at
http://www.lathes.co.uk/perris/ , and still in production as the £2000

Cowells. This has a solid M10 x 1 leadscrew nut, making repositioning the saddle over any distance a pain – 50 turns of a tiny handwheel to shift it 2”. With changewheels set up for fine feed, the motor can be used in forward or reverse to drive it along, but progress is painfully slow. The quickest way is to disconnect the leadscrew dog clutch and use my cordless drill with a dog arrangement to drive the handwheel, but that relies on both on my finding it and its battery being charged, which it often isn’t.
Anyway, being a glutton for punishment, I am making a little apron with a half nut (there isn’t room for a pair of them). I had to make an M10 x 1 LH tap, but that’s another story. The half nut is basically done. A steel pin will project from its underside, and bear on the circular ramp on the cam, so that moving the cam a quarter turn will lift the half nut into engagement. A spring will disengage it when the cam is moved the other way.
There are easier forms for such cams (see
http://lathes.jrbentley.com/leadscrew.html , half-way down), but I like a challenge. I have no CNC, and don’t even possess a rotab for my mill, but I do have another larger lathe with a QCTP. One of the toolholders is a crude home-made affair with a 1/2” hole for boring bars. I also have an old, slightly worn Perris spindle, 1/2” OD:
Could these be the makings of a toolpost spindle to mill out the cam? Yes, they could; the spindle fitted the hole well, rotating nicely with no discernible radial play. With the clamp screw removed, copious oil could be administered through the holes. The only new part which had to be made was a collar and setscrew added to control end float. With a little Perris/Cowells collet chuck to hold an end mill, the contraption was good enough for a one-off job:
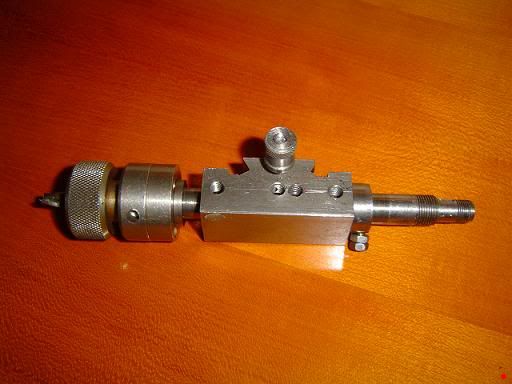
The garage yielded a Black & Decker drill, and a flexible driveshaft with a chuck big enough to grab the far end of the spindle. The whole assembly was set up on the lathe; here, the orange end of the bendy driveshaft is visible, the drill being off-stage to the left:
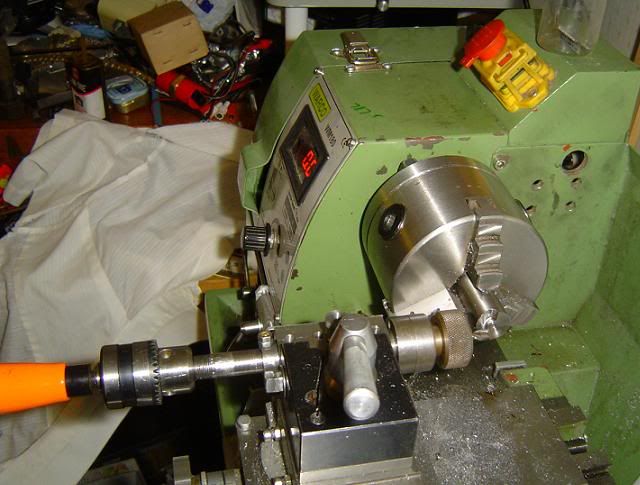
The tooling was ready, but how to generate the cam?

I wanted a quarter turn to lift/lower the half nut by about 1/8”, and the cam would look like a fragment of a square form 2TPI thread. The lathe was set up for 2TPI. The overall 1 to 5 ratio of the changewheels from spindle to leadscrew made it impractical to turn the lathe chuck by hand, but manually turning the leadscrew reversed the ratio to 5 to 1 and rotated the spindle while simultaneously moving the saddle and tool. The topslide was set parallel to the ways, to advance the cutter in between taking repeated light cuts. A saddle stop was fitted to halt each successive cut in the same place.
I gripped a length of 3/4" silver steel (drill rod) in the lathe chuck, and nervously went on the attack. Amazingly, it seemed to work! I don’t know what the digital camera equivalent of shutter speed is called, but it’s damn fast – this shot was taken with the spindle doing about 1000 rpm:
After drilling a hole for a spindle, the disc I wanted was parted off and generally cleaned up ready for hardening. The surface finish on the ramp isn’t brilliant, due to general lack of rigidity (and possibly to the flexy drive, which is a long spring in a cover, winding and unwinding during cuts), but the cam will be fit for purpose. I know you have seen this pic before, but a repeat will save wear on your mouse:
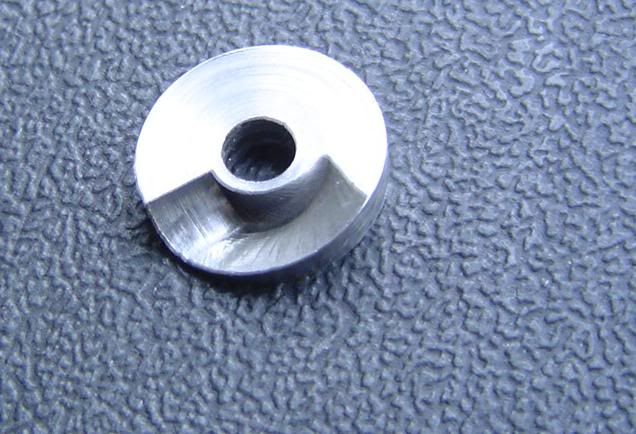
Of course,
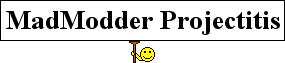
has now set in, but any ideas about making a real milling spindle which fastens direct on the topslide in place of the QCTP for rigidity, and has proper bearings, will have to wait their turn.
Andy