I've been meaning to make a grinding rest since I bought a grinder but have managed with freehand grinding. I've been spurred into action by noticing the tearing on one flank of a thread I was cutting and decided that the remedy was more accurate tool grinding.
I looked at some designs many of which seemed overcomplicated, and most needed resetting to the wheel after adjusting the angle.
I thought it might be possible to make one that would stay set to the wheel as you adjusted the angle by making the edge nearest the wheel the centre of rotation for angle adjustment.

I thought about adding pivots to the side of the rest but realised they would have to stick up above the surface and may get in the way.

I thought about a curved slot (and even drew it) before I realised that it would tend to pivot about the bolt rather than slide in the slot.

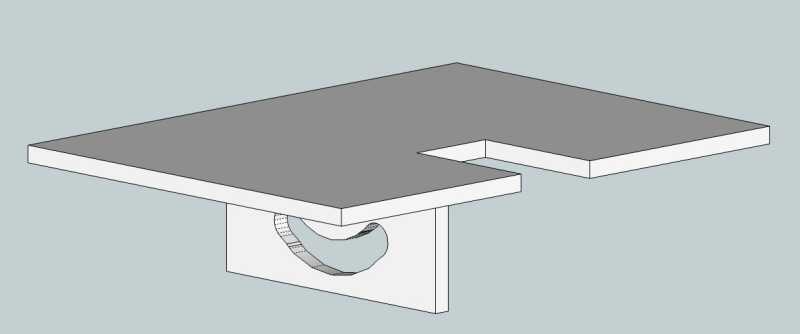
I thought about half a tube resting on two support rods with a clamping rod inside before I realised that the rods would have to go through the grinding wheel.

I've finally come up with a design I'm going to try. I don't know if it's original but I've not seen one like it. There may be a good reason for that.

First I drilled two holes in a 2.25" piece of 1" angle and used them as guides to drill another piece of angle and two scraps of the steel I plan to use for the top of the rest.

Then I bolted them together, set them up in the lathe and turned them to 2".
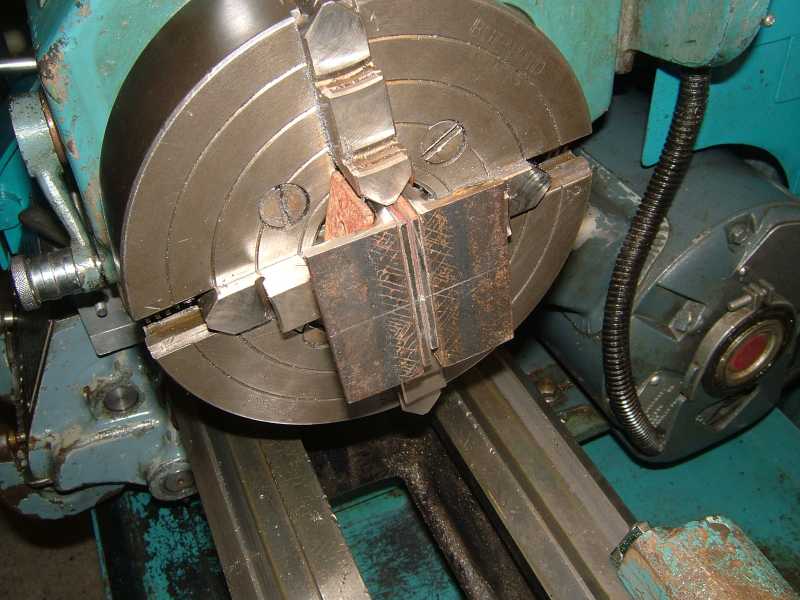
I filed the edges to match as these are not critical.

This was the result.
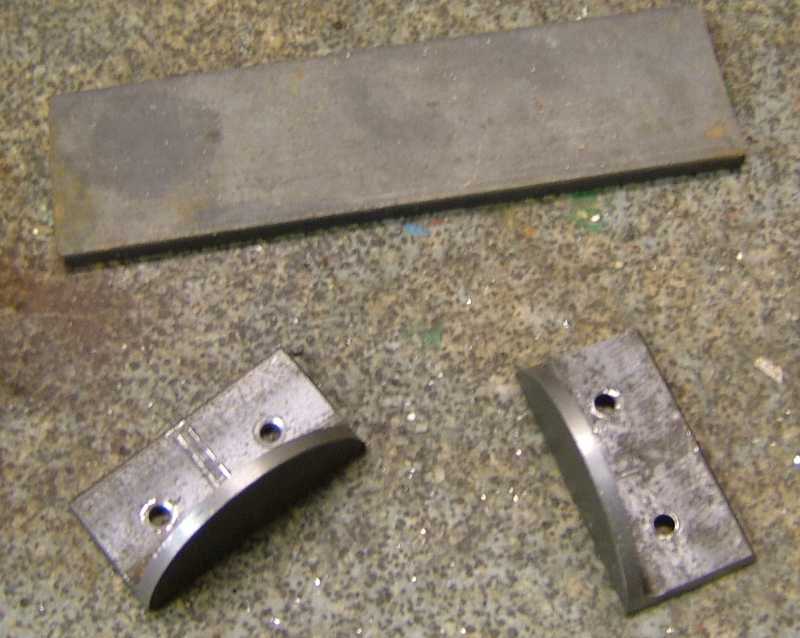
I took a couple more pieces of stock and drilled and tapped some holes.
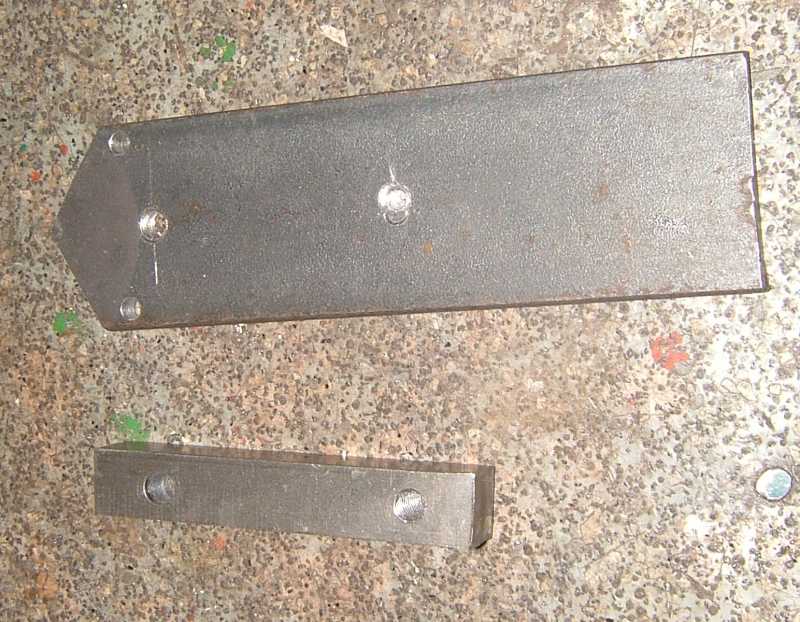
Then came the trial assembly. Here is the progress so far.
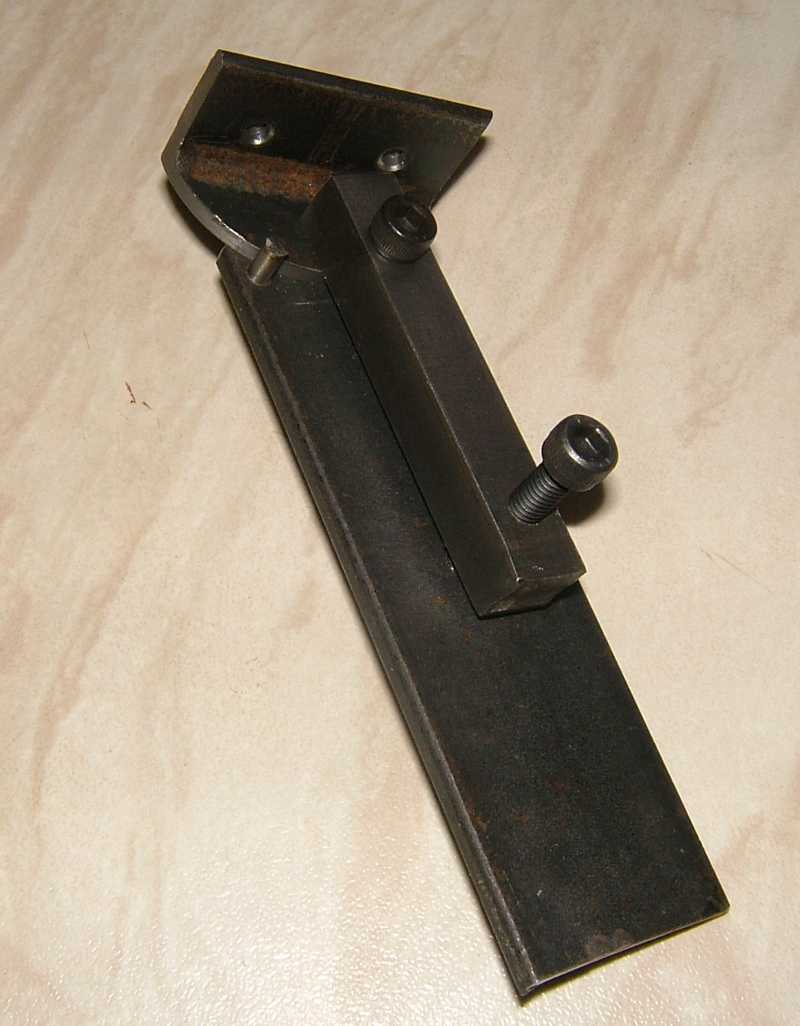
The square stock and the bolts are configured like a toolmaker's clamp and when slackened the angle slides on the two pins inserted in the upright. It looks like it might work, I can tighten it with my fingers just enough to lock it solid and the angle adjusts OK. The upright is too thin as it tends to bend under the clamping force and I could get the mounting nearer the centre of the top plate without fouling the grinding wheel if I configure the clamping screws to work from the other side.
More to follow soon (I hope).

Russell