I have been playing with my 3d printer I have seen a utube video a while ago using pla plastic to cast metal. The finishes on the castings seem quite good but they say to burn out the plastic (2 - 4 hr's) then give it a shot of air to clear the residue.
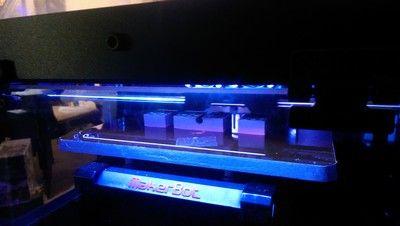
I have found this molding rubber at PMS Hobby it melts in the microwave and can be used for internal or external molds it is soft and spongy and I figured if it isn’t ridged enough I could pierce it with thin brass rod or tubing that should melt into the pour it is more ridged when cold.
http://www.composimold.com/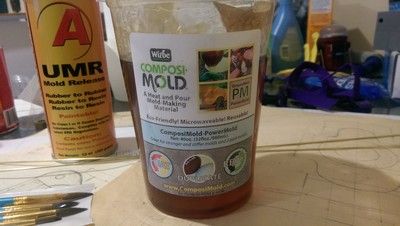
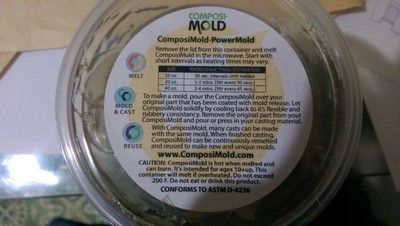
So this is a 5 piece mold that I made, the 3 main parts are on the bottom with two glands one on each side, the top piece wasn't really necessary but I made it anyways it’s a gate connecting the two glands for pouring.
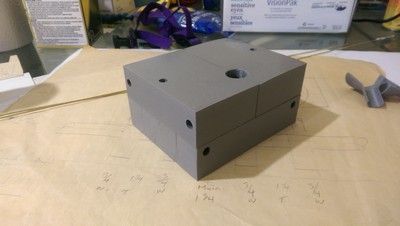
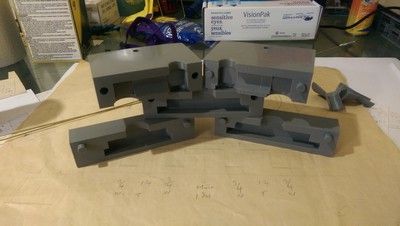
I didn't use any release agent on the first attempt and it didn‘t release very well, on the second I used pam cooking spray wiping off the excess spray making removal of the cast possible.
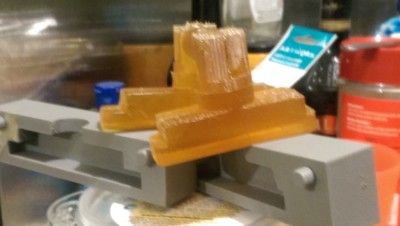
As you can see there is some leakage at the seams but it is quite thin and easily removed the glob on top is from the funnel I printed it in two halves (it leaked) the idea was to use it for a sprue it’s walls should have been thicker.
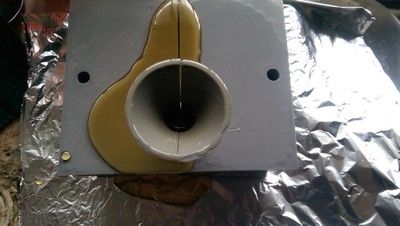
I could have used threaded rods to press them together as the pin holes go straight through but for coming straight from the printer (including pins) I'm impressed how well it seals.
I'm going to try casting brass and see how it goes.
Here is the rubber set in plaster /sand a 50/50 mix when it dry's out I'll melt out the rubber (200 degrees F) and open up the passage a little for the pour with a rasp I don’t think I‘ll need a riser as the brass is quite heavy.
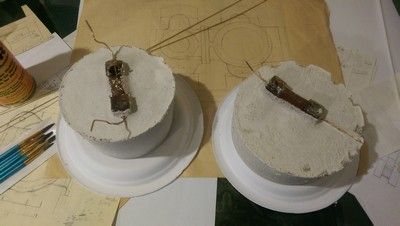
I’ll let you know how it turns out!