I have the column and knee sorted now, still more flex than I would like but it seems to be a FEATURE of this machine. Will have to see how that translates into the quality of work I can get out of it.
Next up is finding out the error in the horizontal spindle position. First job check my table is tracking level in Y
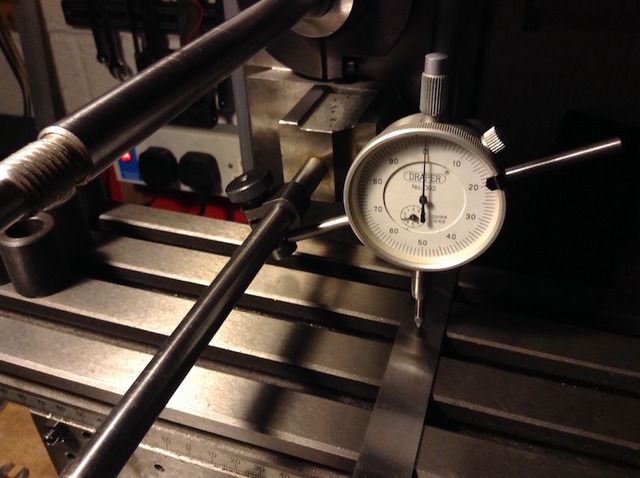
Happy with that, 0 end to end, now to clock the horizontal spindle after clocking it runs true along in's length, and it does.
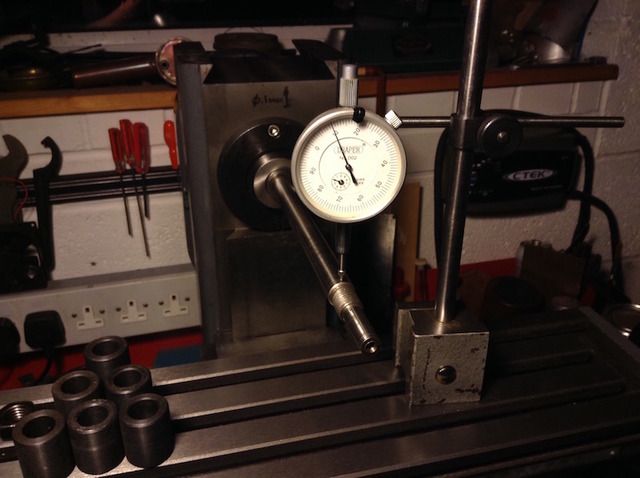
The spindle is pointing up 0.1mm over 170mm of travel.
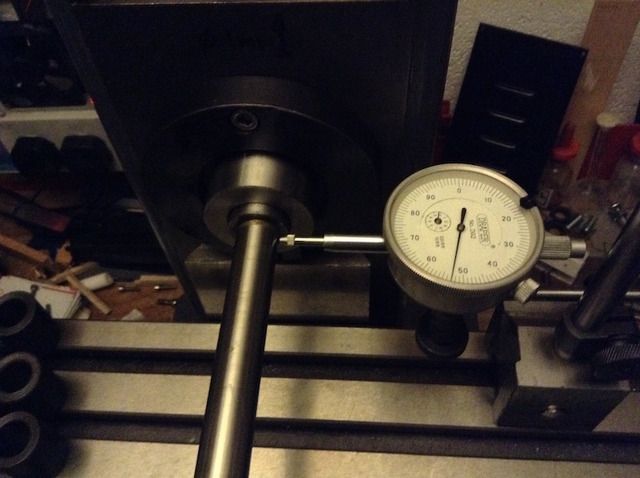
OK I screwed up as I should have zeroed from the spindle out but zeroed at the end of the spindle and clocked inwards. Thats 0.47mm pointing right

again over 170mm, not as bad as I was expecting, but still plenty to give the overarm bearing a hard time, not to mention the unnecessary load on the spindle bearings.
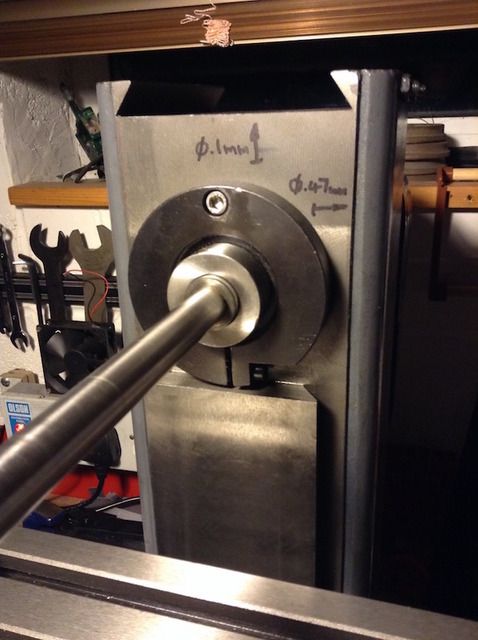
So this is where I am up to now, I need to turn a small shaft or mount my laser alignment tool in the overarm bearing to check the spindle centre is where it should be and that the runout is at the rear, as it appears to be in the casting. Work out a plan and do another tear down, I think I can do this in my sleep now.
I just realised this should probably have been posted in Project Logs till I get to the actual CNC conversion. Hope it's useful info for someone.