
Robert, it works

.

Snapped a 1/4" bit ? - that sounds like a tiny bit of over-enthusiasm was used

- best lighten up a bit on the cuts

. At 2C without a coat you're getting on to Geordie territory - are you sure you're from the States ?

--

Just poking a bit of fun at you; I know you're making chips other than the kind one eats

. PS I'm glad I'm not close enough to hear the "owl"

Rob, cheers mate

- I'll have to get the wee 'un to climb on a scale the next time I see it... might measure 0.5 gram across the top and bottom legs

.
DMIOM (I wish I had a more conventional first name to address you with

) At least it's not packing any "heat", so it's in effect un-armed completely... I refrained from offering it a sip from my drink; that would turn it completely legless though...

After a very merry week

, it was nice to get to the shop today.
I first did a C-o-C, then decided on an end mill size and then added a's, b's, thetas and so on, then used sines, cosines and other stuff to make some calculations:

Yes, yes, I know... Boring math stuff; I'm a sucker for punishment

- but then again, it's really not that hard to do, and very useful

On to machining then. I screwed the chuck to the rotary table and centered it on the mill with a 6mm bar chucked up - close enough for machining flywheel webs:
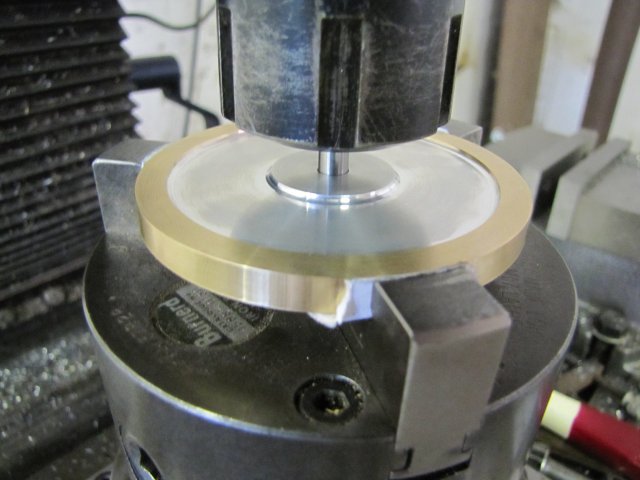
The X and Y hand wheels were zeroed here, and I just kept notes on the "boring maths page" (BMP from now on!) to remember which way I was cranking to compensate for backlash.
Then I drilled a bunch of 3.5mm holes according to the BMP:
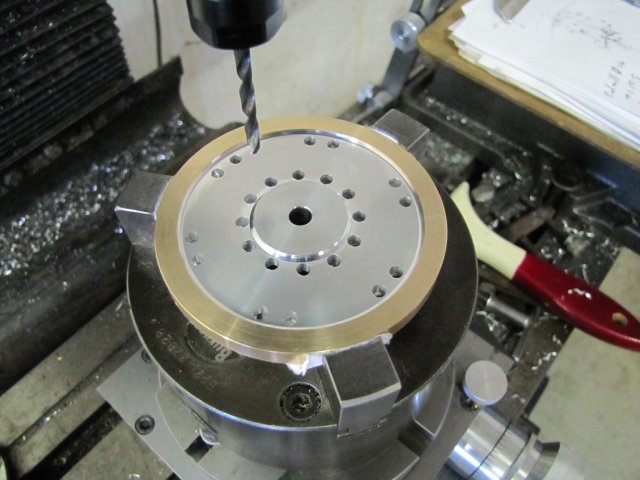
I want to finish off the webs with a 4mm end mill, so I used the 3.5mm drill as it leaves a bit of lee-way for error, and can just be drilled without using a center drill (or even better a spotting drill) for each location. If the 3.5mm drill wanders a tiny bit, that's OK.
Next I marked out the sections that must be milled out - just to help prevent a brain-fart later:
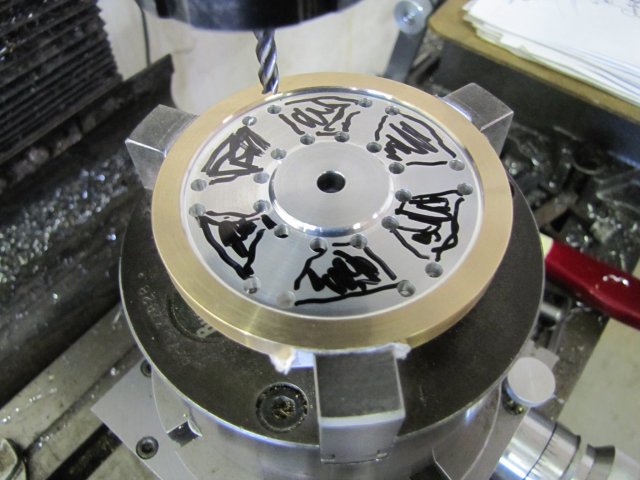
And a-milling-we-went. First the insides radial edges closest to the hub, with Y offset for the radius and feeding the rotary table between angles - taking the readings off the BMP; 1mm deep Z for each pass requiring 4 passes per slot; no use to hog things out, as that could just end in heartache or lots of "bad" words from a variety of different languages - or both:
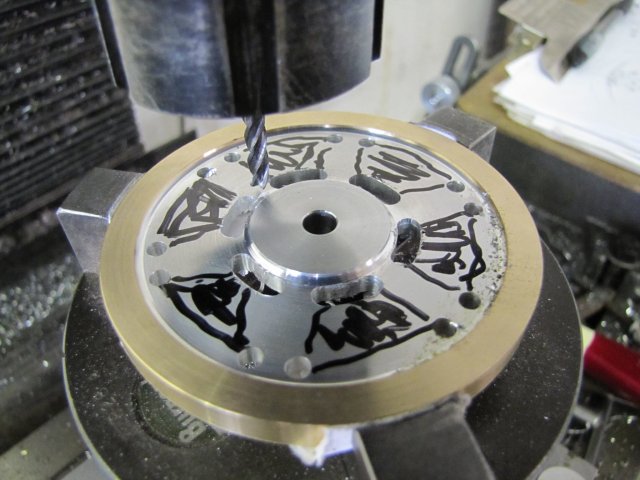
The outside radial edges followed using the same method:
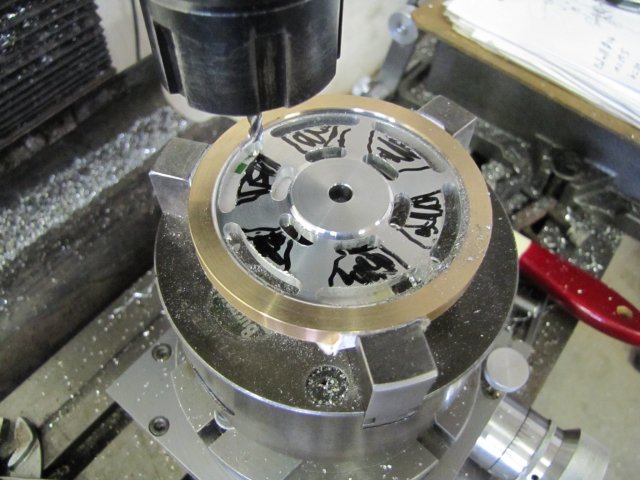
Up to now, everything was done from the mill table's X zero point with only Y feeds for offsets. For the next step, I once again referred to the BMP, offset the mill table in X and Y accordingly, dialed in the needed angle on the rotary table, and started on the straight sections of the webs - with feed on Y only:

More reference to the BMP, other offsets on the mill table, and the last cuts were done:
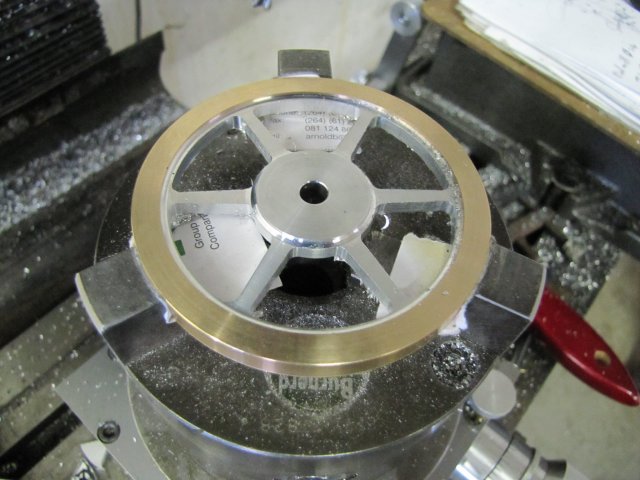
One side of the flywheel rim was still sharp from previous machining, so I mounted a bit of 6mm silver steel in the collet chuck on the lathe, pushed a bit of cardboard over it to protect and drive the flywheel hub, and then used a cone center with another bit of cardboard on the revolving tailstock center to mount the flywheel:
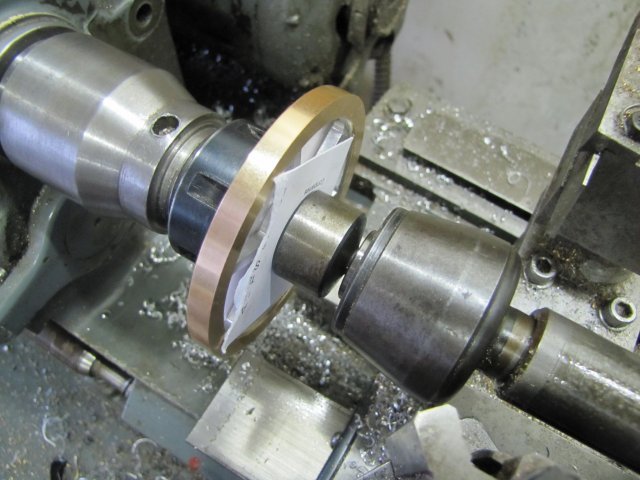
A quick lick with a file cleared off the burr on the rim, and then I just did some light file-work to get rid of burrs on the flywheel web. A final rub with some emery paper rolled into a cylinder removed some more toolmarks, and I ended up with this:
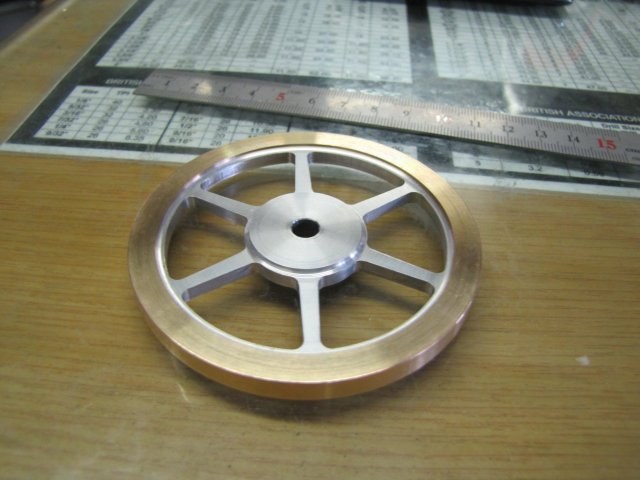
An OK-sort-of-looking flywheel. I wanted lightly tapered spokes, but not too lightly tapered either. Unfortunately, this is toward the "too lightly" side, so a lesson I can take forward. 4 degrees taper is too little on relatively short spokes like these

. I'm not about to use some form of put-on-tool to correct this; in fact the only put-on-tool I have that is suitable for this application is called "re-make"

.
The BMP did get some additional scribblings on it through the process... Yes, I KNOW... It's still a "Boring Maths Page", but it did help

:
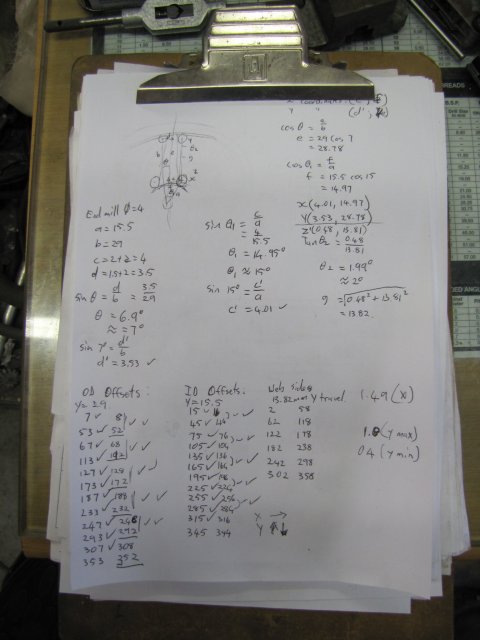
In fact, if I had to be more mathematically precise, there would have been a lot more calculations involved - but this was good enough for the job on hand.
The flywheel does fit on the base though, and looks OK. I was thinking about painting the webs, but I have a hunch that will not be done; I'll decide about that once the base is painted:
Merry Christmas Everyone!Kind regards, Arnold