Thanks Jim

- I find that tooling plate invaluable now; in fact, at some point I want to make up some more of them and a lot more clamping kit. If you're interested,
here's a link to how I built it, as well as good advice from other home engineers.
John, Thank you

Today was one of those golden days in the shop that makes me love model engineering so much. Just the right amounts of challenges, head-scratching, problem solving, lots of chips, and that whole kaboodle coming together in a nice end result. Not really much to show as the end result, but the journey was the fun part.
For the next step in the machining process, I needed a sacrificial plate. A bit of flat wood would have done as well, but I wanted slightly more accuracy than the wood would have given. A while ago, the storage term for a whole lot of these ran out at work:
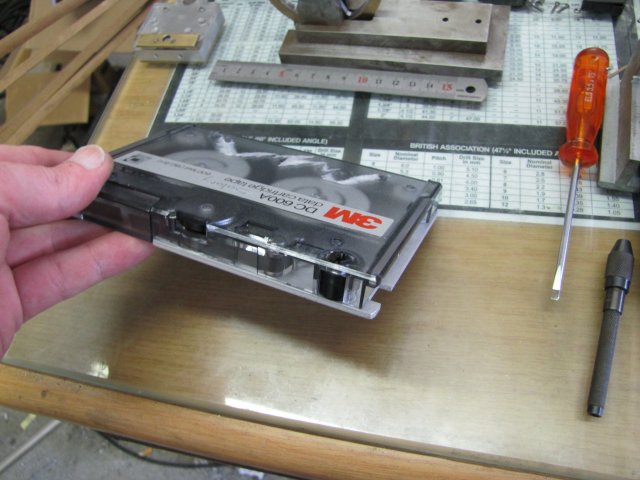
Anybody remember those? As I'm responsible for IT Security at work, I signed them off for responsible destruction - told the bosses what would happen to them, and brought them home. Taken apart, it's easy to snip the tape into thousands of pieces, and I get nice bits of tempered aluminium plate and a lot of precision pins out of them to use in projects. Bosses are happy, and so am I.
I was spoilt for choice on how to do the next part... Work on the lathe face plate, or boring head on the mill... As there was quite a bit of milling to come, I decided on the face plate, as it's fun to change between machines for different jobs.
With a suitable bit of plate sawn from the old tape, I started setting up things on the face plate. I find it easier to start setup on a table, and then mount the face plate to the lathe later:
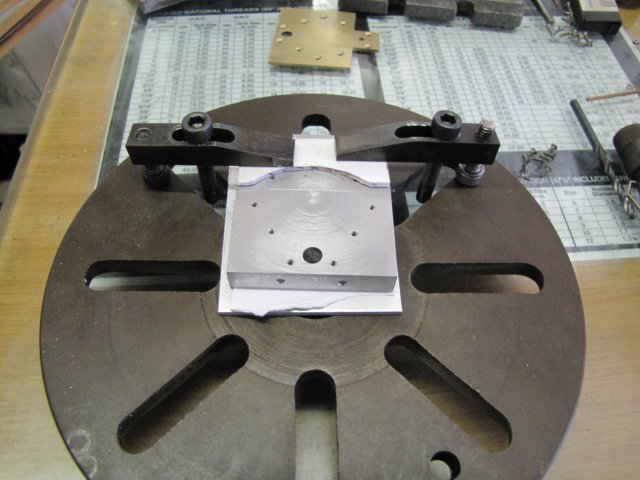
For the next step, the lot had to be mounted on the lathe, with the workpiece centered on the reamed hole. Normally that would be done by sticking a pin in the hole and using a dial indicator or DTI to clock it up, but I know a pin chucked up in my lathe's tailstock is spot-on, so that's the method I used. Face plate mounted on the lathe and the pin in the chuck:
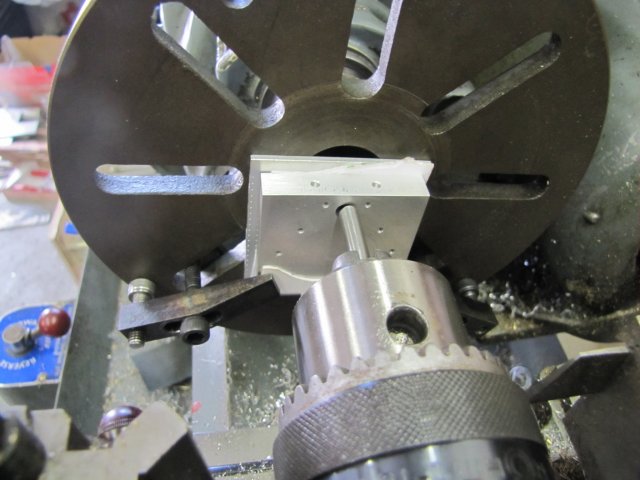
Not a bad job of eyeballing on the table before-hand

With the workpiece loosened slightly, it was easy to lightly tap it into position to fit the pin:
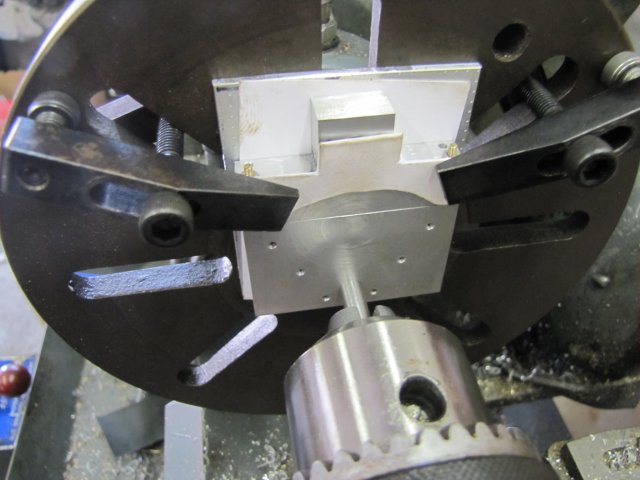
Then I added one more clamp - just to be safe, and to allow me to remove either of the side clamps so that I could get at the screws holding the engine body to the top:

I'd forgotten to lay out the cut dimension for the top... Not so easy with a hole where the center should be either... The small lathe is not mounted properly yet, but this is a very light job, so I fired it up and faced and lightly center drilled a bit of 6mm rod:
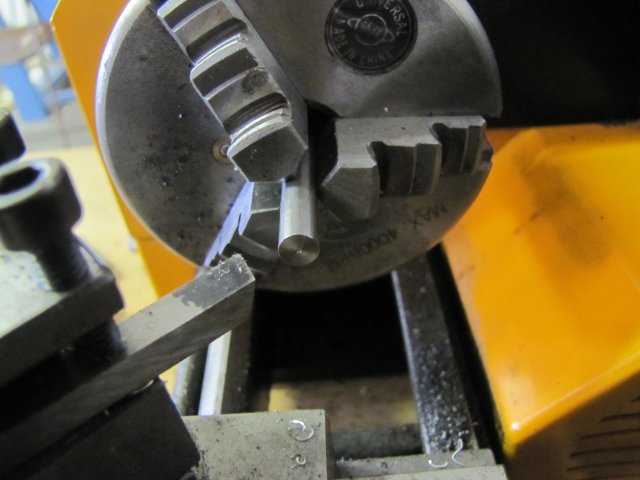
That was then sawn off and inserted in the hole in the block:
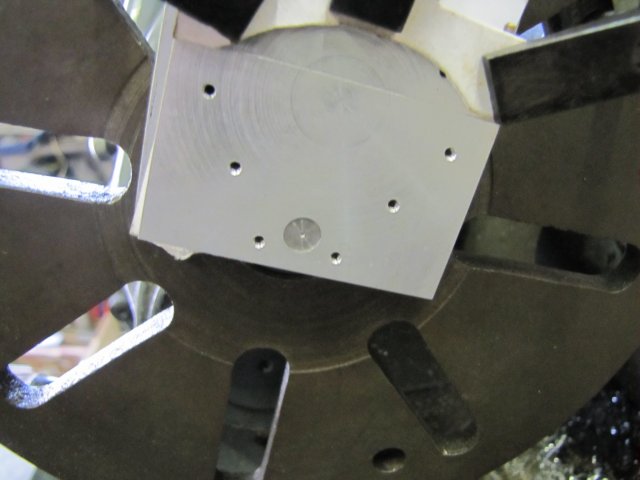
Next, I set my compass to 31.75mm. Well, the photo shows that it was slightly less than that, but the camera's macro mode is much better than my eyeballs. The reason the reading on the rule is 41.75mm is that the other end of the compass is sitting in the 10mm groove of the rule:
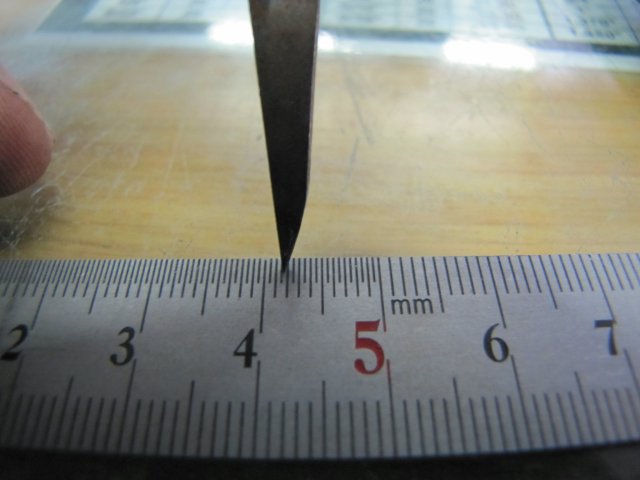
Target cut-line scribed:
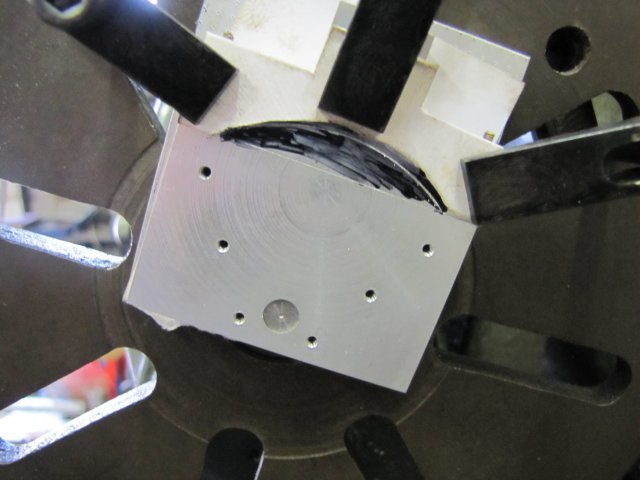
Then I added some counterweights to the face plate; No fancy math was used; just the fact that I have a fairly good feeling for how heavy the bunch of clamps and retaining nuts are - the gears were selected to approximate that. And a final check from the top as to whether there would be any clearance issues:
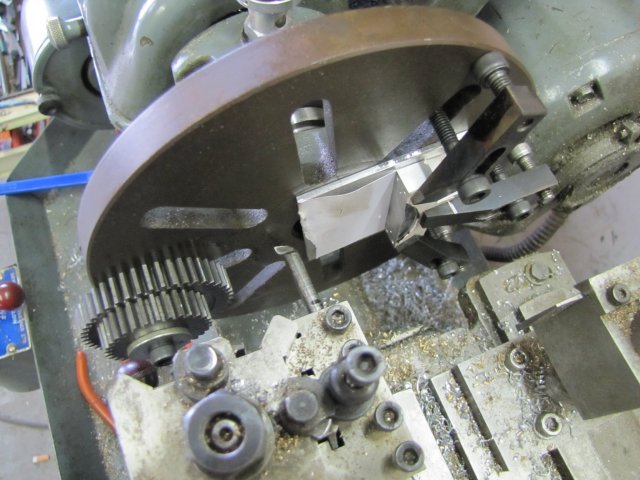
And a view from the side - with the cutting bit set as deep as it would go:
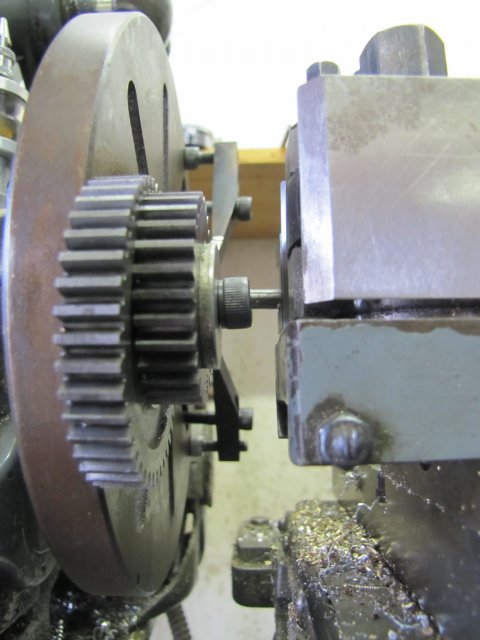
Then I started putting some cuts on... The cutting bit was honed super-sharp, but on the second cut I heard the dreaded sound... A high-pitched squeal each time the cutter cut... Chatter... Stopped, and yes there it was (you can click on the image for a larger picture):
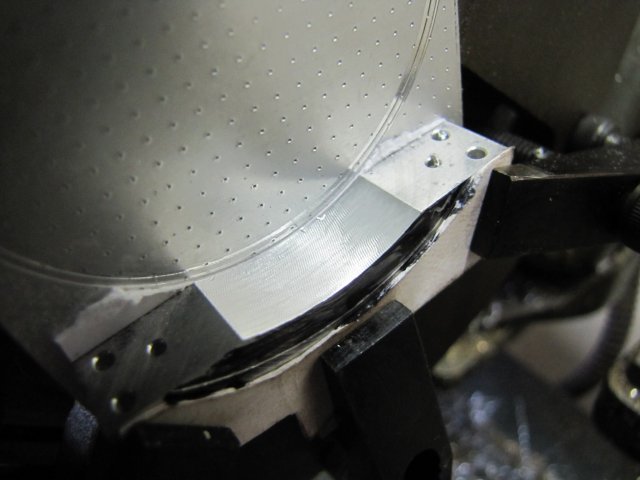
The finish in this cut must be smooth as silk; there would be no easy way to lap it accurately once done... So I tried a stiffer toolbit; same thing - slightly finer chatter, but still there.
As the chatter was very fine, it would not take much to damp; I tried pressing on the back of the toolbit during the cut with a toothbrush handle, and the chatter went away

:
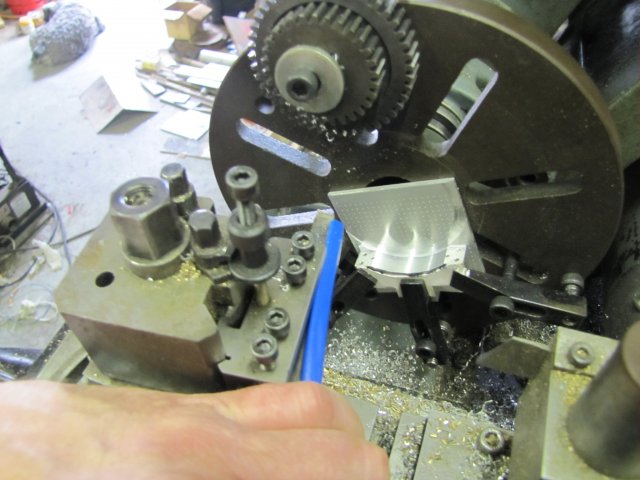
After the final cut with the toothbrush in position (once again, clickable for a larger photo):

That's the finish I was after

Some more lay-out followed:
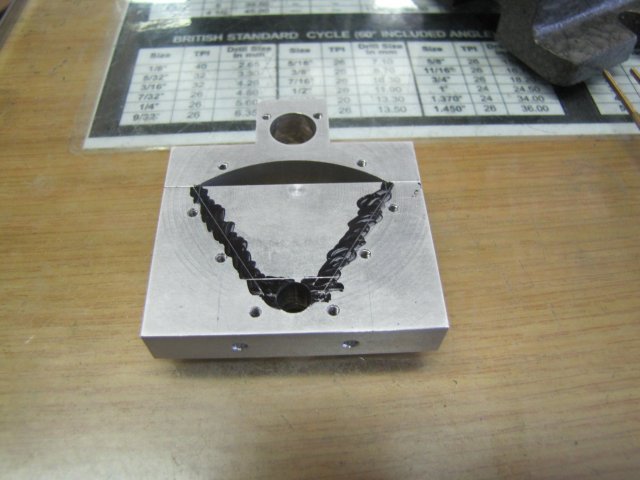
Then a quick bit of hogging in the mill:
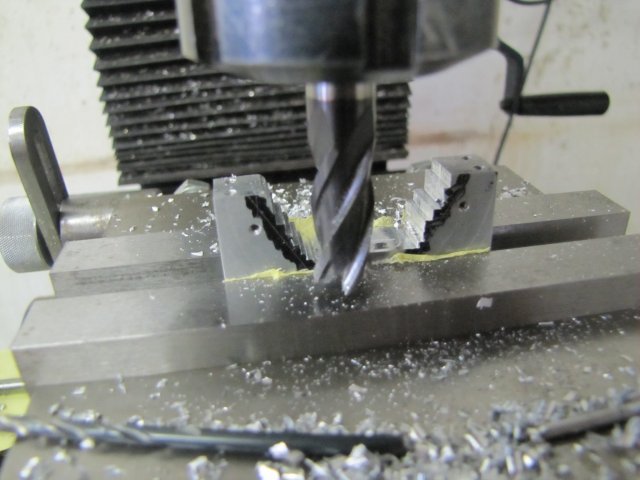
I just used some threaded rod screwed into the mounting holes to set the piece to mill out the angled sections:
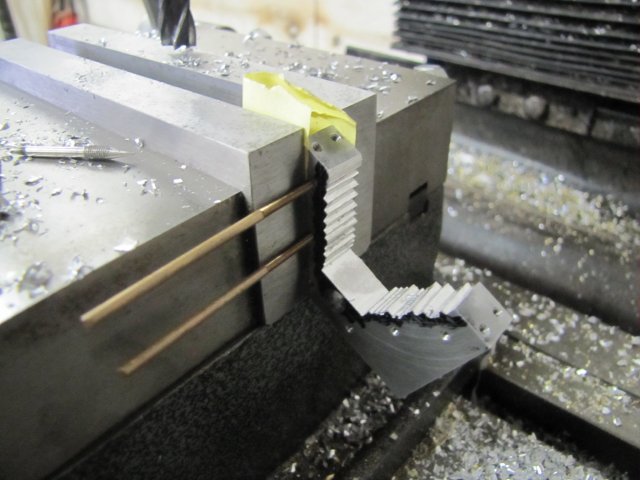
A little while later:
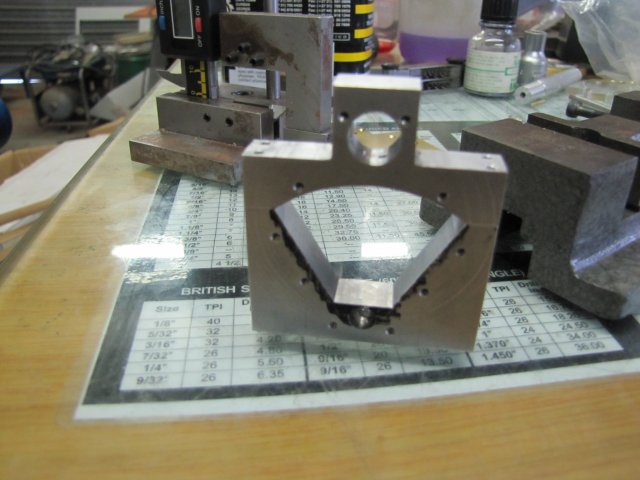
Then with both covers mounted on, a bit more lay-out:
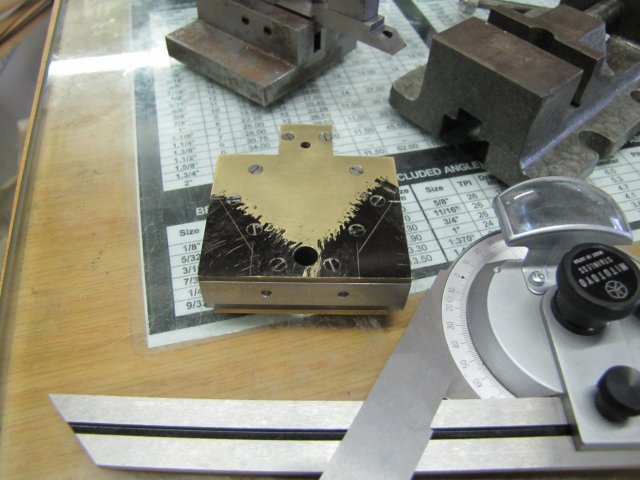
More milling - a bit more careful this time so as not to break out chunks of the perspex - and lots of brass, aluminium and perspex chips all over the show:
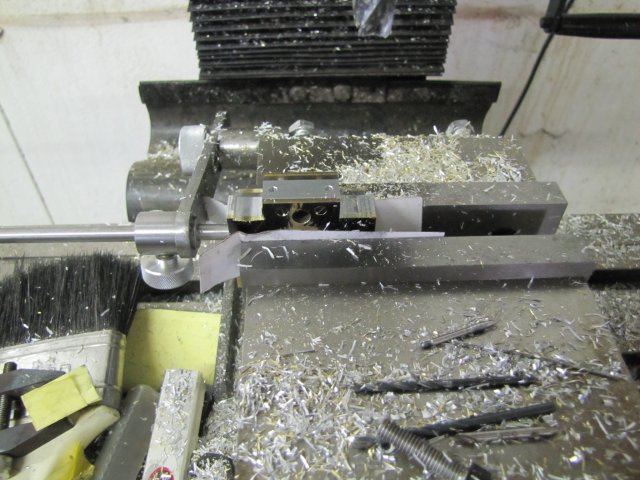
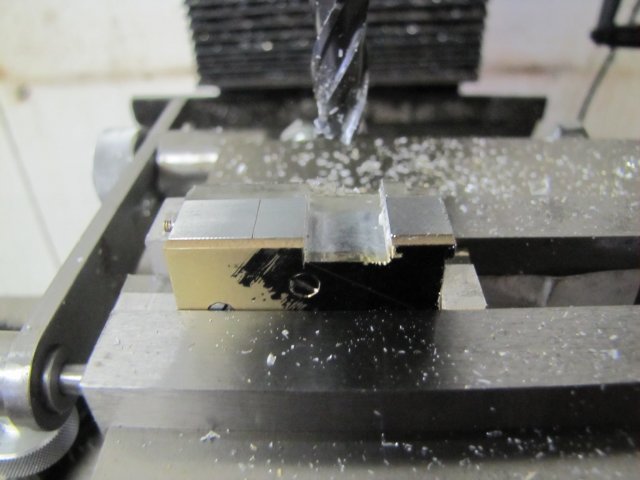
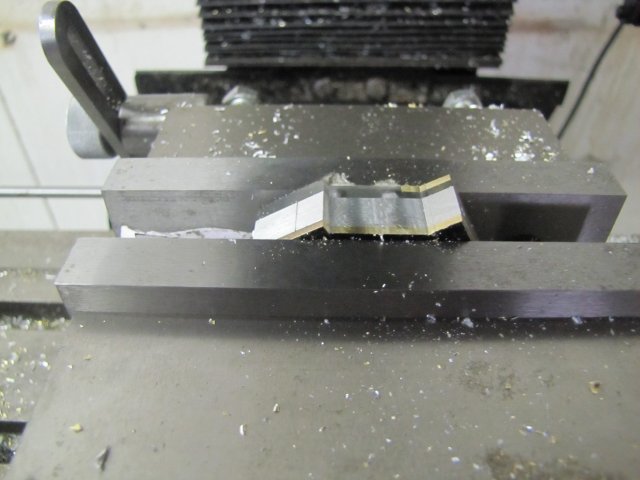
Finally I ended up with this:
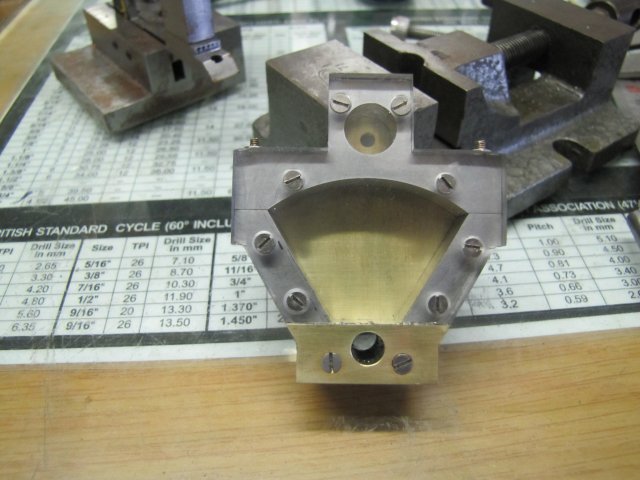
I left the outer edges of the block slightly thicker than the plans show - they are purely cosmetic, and the extra thickness is to help prevent the perspex from cracking.
Overall progress:

Looks more like it. There's still some work left on the block - a hole to drill and tap in the top for air supply, and a bit of clearance milling on the bottom for the vane - then a final flat-lap and cosmetic work, but the hardest part is over.

, Arnold